生産管理システムとは?
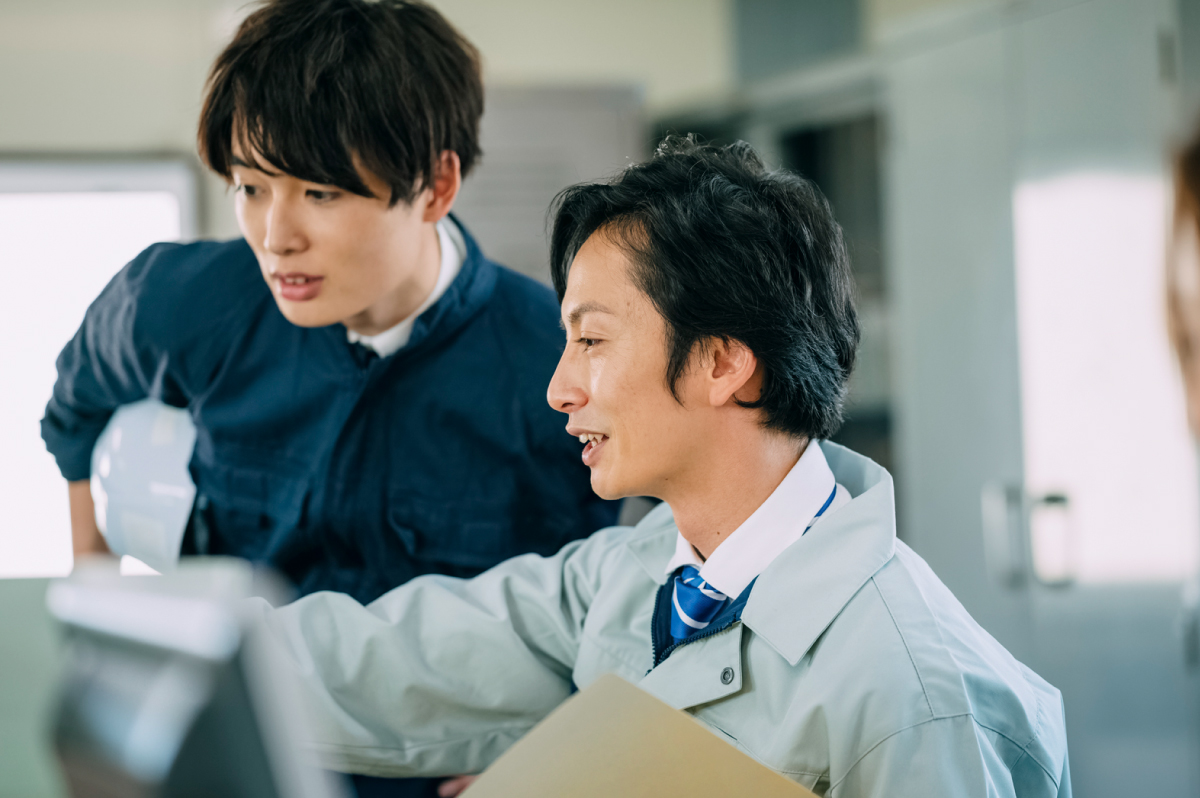
製造業における効率化や生産性向上が求められる現代、「生産管理システム」という言葉が注目を集めています。
本記事では、生産管理システムの基本的な概要からその役割、導入による具体的なメリット、そして選定時のポイントまで、詳しく解説します。
製造業の現場で「生産管理」の重要性を理解し、適切なシステムを選ぶ手助けとなる情報を提供します。
生産管理システムとは?
生産管理システムとは、製造業の生産プロセスを効率化し、全体の流れを最適化するためのソフトウェアやツールの総称です。このシステムは、以下のような業務を統合的に管理します。
受注管理
顧客からの注文内容を迅速かつ正確に把握し、製造プロセスに反映します。注文履歴や顧客情報と連携し、リピート注文や個別対応の効率化を実現します。これにより、納期遅延を防ぐと同時に、顧客満足度とリピート率の向上が期待できます。
生産計画
生産量やスケジュールを立案し、製造現場における作業の効率化を支援します。需要予測を基にした柔軟な計画立案が可能で、繁忙期や季節性の需要にも迅速に対応できます。また、生産設備の稼働率を最大化することで、コスト削減と納期遵守を両立させます。
在庫管理
原材料や製品在庫を適切に管理します。リアルタイムな在庫データの可視化により、過剰在庫や欠品を防ぎます。さらに、在庫回転率を向上させ、倉庫スペースや運用コストの最適化を支援します。購買部門との連携により、ジャストインタイム調達の実現も可能です。
工程管理
製造工程の進捗状況をリアルタイムで監視し、ボトルネックや作業遅延を早期に発見します。各工程のデータを分析することで、生産性向上のための改善ポイントを明確化します。また、異常発生時には即座に通知され、迅速な問題解決をサポートします。
品質管理
製品の品質チェックを一元管理し、不良品の発生を最小限に抑えます。製造履歴や検査データを蓄積することで、問題発生時の原因特定や再発防止策の立案が迅速化します。これにより、顧客クレームの削減や信頼性の向上が実現します。
原価管理
製造にかかる直接コストや間接コストを詳細に分析し、利益率を最大化するためのデータを提供します。製品ごとの採算性を可視化し、収益性の高い製品やプロセスにリソースを集中させることで、経営判断をサポートします。
これらを一元的に管理することで、製造現場の可視化が進み、業務の効率化とコスト削減、さらには生産性向上が期待できます。また、生産管理システムは多品種少量生産やカスタマイズ製品の需要増加といった現代の製造業のトレンドにも対応しています。さらに、生産管理システムは、サプライチェーン全体の最適化やリスク管理にも寄与します。例えば、予期せぬ需要変動や供給遅延に対しても、リアルタイムでデータを可視化し、迅速な意思決定を支援します。この柔軟性により、製造業全体の競争力が大幅に向上します。生産管理システムは、単なるデジタルツールではなく、製造業の持続可能な成長を支える戦略的な基盤として機能します。そのため、適切な導入と運用が企業の成功に直結する重要な要素となっています。
生産管理システムとMES(製造実行システム)との違い
生産管理システムとMES(Manufacturing Execution System: 製造実行システム)は混同されることがありますが、それぞれの役割には明確な違いがあります。
生産管理システム
- 主に計画・管理レベルを担当
- 生産計画や在庫管理、原価分析など、製造全体の最適化を支援
- 経営層や管理職向けの情報を提供
- サプライチェーン全体の連携や長期的な経営戦略の支援にも注力
MES(製造実行システム)
- 現場実行レベルを担当
- 生産ラインのリアルタイムモニタリングや機械の稼働状況、オペレーターの作業進捗を管理
- 現場スタッフ向けの詳細な指示や情報を提供
- 現場の作業効率化や即時的な問題解決に特化
両者の連携の重要性
生産管理システムは「工場全体の管理」を担い、MESは「現場での実行」をサポートします。
この両者を連携させることで、製造業の効率化はさらなる高みへと到達します。例えば、生産管理システムからの計画データをMESに送信することで、現場作業がスムーズに進みます。
また、MESから収集されたリアルタイムデータを生産管理システムが活用することで、計画の精度や適応力が向上します。このような連携が、製造業全体の競争力を強化する鍵となります。
生産管理システムの進化と背景
生産管理システムの歴史を振り返ると、その進化は製造業の効率化の歩みと深く結びついています。かつては人手による紙ベースの管理が主流でしたが、IT技術の進歩によりMPS(生産計画システム)やMRP(資材所要量計画)の登場を経て、今日の高度な生産管理システムに至っています。
MRPの登場 :
1970年代には資材の効率的な調達を目的としたMRPが普及し、製造業の生産性向上に貢献しました。
ERPの進化 :
1990年代以降、ERP(統合基幹業務システム)が生産管理だけでなく、会計や人事といった他部門の業務を統合的に管理するようになりました。
業務改善の加速 :
資金面の支援により、業務効率化の取り組みをスピーディに進められます。例えば、最新の自動化設備やデジタルツールの導入により、労働時間の短縮やヒューマンエラーの削減が実現します。また、助成金を活用して従業員のスキルアップを図ることで、人材の生産性向上とモチベーション向上にもつながります。
IoTとAIの導入 :
現在ではIoTセンサーやAI技術を活用してリアルタイムデータを収集し、生産現場の即時対応が可能となっています。
生産管理の重要性
製造業における「生産管理」は、企業の競争力を左右する重要な業務です。具体的には、次のような理由で重要性が高まっています。
市場の変化への迅速な対応
顧客ニーズの多様化や競争の激化により、小ロット多品種生産が求められる現代において、柔軟でスピーディな生産対応が必要不可欠です。
コスト削減のプレッシャー
原材料費やエネルギーコスト、人件費の上昇が続く中、生産プロセスの効率化や無駄の削減を通じて競争力を維持することが求められます。例えば、歩留まりの向上や不良品削減が直接的なコスト削減に寄与します。
品質の向上とトレーサビリティの確保
高品質な製品を安定的に提供することは、顧客信頼の構築とブランド価値の向上に直結します。また、製造履歴の追跡が可能となるトレーサビリティ機能により、品質問題の早期対応が可能になります。
業務の可視化とデータ活用
IoTセンサーやデジタルツールを活用して生産現場のリアルタイムデータを収集・分析することで、ボトルネックの特定や生産計画の改善に役立てることができます。これにより、的確な意思決定が迅速に行えるようになります。
デジタル化とDX推進
製造業におけるデジタルトランスフォーメーション(DX)の実現は、業界全体で急務とされています。生産管理システムは、IoT、AI、クラウド技術などと連携することで、製造現場のスマート化を支援します。これにより、競争力を高めるための新たな価値創造が可能となります。
リスク管理と持続可能性への対応
パンデミックやサプライチェーンの混乱など、外的リスクへの迅速な対応が求められる中で、生産管理システムはリアルタイムのデータを基にしたリスク回避策を提供します。また、環境負荷の低減や持続可能な製造プロセスの実現にも寄与します。
製造業における生産管理は、効率化やコスト削減といった基本的な目標を超えて、長期的な競争優位性を築くための基盤となっています。
生産管理システムの主な機能
生産管理システムには、多岐にわたる機能が備わっています。以下に、主要な機能を詳しく説明します。
(1) 生産計画機能
生産計画機能は、顧客からの受注データを基に最適な生産スケジュールを自動で作成します。この機能は、リードタイムを短縮し、効率的な生産を実現します。また、需要の急変や生産設備の稼働状況を考慮し、柔軟に計画を調整できるため、リソースの最適化が可能です。
(2) 在庫管理機能
原材料や製品在庫を適切に管理する機能です。在庫過多や不足を防ぎ、資金効率を高めるだけでなく、必要なタイミングで必要な量を調達する仕組みを整えます。これにより、生産ラインの停止を防ぎつつ、倉庫コストの削減も実現します。多品種少量生産の現場では特に有効です。
(3) 工程管理機能
製造工程の進捗をリアルタイムで可視化し、ボトルネックの特定や作業効率の改善をサポートします。各工程での生産データを収集することで、生産サイクル全体を最適化し、生産性向上につなげることが可能です。また、異常発生時には即座に通知され、迅速な対応を可能にします。
(4) 原価管理機能
製造にかかる直接コストや間接コストを詳細に把握し、最適なコスト配分を実現します。これにより、製品ごとの利益率を明確にし、採算性の高い生産計画を立てることが可能です。また、原価構造を分析することで、さらなるコスト削減の施策を見出す手助けとなります。
(5) 品質管理機能
製品の品質データを一元管理し、不良品の発生を最小限に抑えます。製造工程でのリアルタイム品質チェックに加え、不具合発生時の原因分析や対策立案を迅速化します。また、顧客クレームの削減や信頼性向上に寄与し、製品価値を高めます。
(6) トレーサビリティ機能
製品の製造履歴を追跡できる機能で、品質問題やリコール時の迅速な対応を支援します。具体的には、使用した原材料のロット番号や加工日、担当者などの情報を簡単に検索可能です。これにより、サプライチェーン全体での透明性を高め、顧客からの信頼を向上させます。
(7) データ分析・レポート機能
収集された生産データを基に、現場のパフォーマンスを分析し、問題点を特定する機能です。これにより、現場の改善活動を加速させることができます。カスタマイズ可能なレポート機能により、経営層や現場担当者に適した形で情報を提供できます。
生産管理システム導入のメリット
生産管理システムを導入することで、次のようなメリットが得られます。
効率化の実現
各業務を自動化・一元化することで、無駄な作業を削減できます。これにより、業務時間の短縮とリソースの最適化が可能となります。
生産性向上
作業の進捗状況をリアルタイムで把握できるため、迅速な対応が可能となり、生産性が大幅に向上します。特に突発的な変更や緊急対応が必要な状況でも柔軟に対応できます。
コスト削減
在庫の適正化や工程の効率化により、不要なコストを削減できます。また、リードタイムの短縮や無駄な作業の排除により、全体的なコスト構造を最適化できます。
品質向上
品質データの一元管理により、不良品の発生を最小限に抑えるだけでなく、製品全体の信頼性向上につながります。これにより、顧客満足度を向上させ、長期的な取引関係を構築する助けとなります。
業務の可視化
データが統合されることで、経営層から現場までの情報共有がスムーズになります。これにより、意思決定のスピードが向上し、計画的な業務遂行が可能となります。
リスク管理
サプライチェーンの混乱や製造トラブルに対する迅速な対応が可能です。特にパンデミックや自然災害といった予測不能な事態においても、データに基づくリスク対応策を立てることができます。
環境への配慮
資源の適正利用や生産過程の最適化により、環境負荷を低減します。これにより、持続可能な経営と企業の社会的責任(CSR)の実現を支援します。
生産管理システム導入のプロセス
(1) 現状分析と課題の特定
生産管理システムを導入する最初のステップは、自社の現状を正確に把握し、課題を特定することです。このプロセスでは、次のポイントを明確にします。
- 生産プロセスの課題: ボトルネックの特定、無駄な作業や非効率な工程の洗い出し。
- 従業員の意識調査: 現場での課題認識や改善希望をヒアリングし、現場のニーズを反映。
- 経営目標との連動: 生産性向上やコスト削減など、システム導入で解決すべき目標を明確化。
(2) ベンダー選定
適切なベンダー選定は成功の鍵です。以下の観点を基に評価します。
- 業界実績: 自社と同じ業界や規模の企業での実績があるか。
- 機能の柔軟性: 自社の業務プロセスにカスタマイズできるか。
- サポート体制: 導入後のトラブル対応や定期的なアップデートが提供されているか。
- コスト: 初期費用、運用コスト、保守費用のバランスが取れているか。
(3) 試験運用(パイロットプロジェクト)
試験運用では、システムの有効性を確認するとともに、導入時の潜在的な問題点を洗い出します。
- 対象部門の選定: 最も課題が顕著な部門や少人数で運用できる部門から試験導入を開始。
- 効果測定: 導入前後の生産性、コスト削減効果、品質向上などを定量的に比較。
- 改善提案のフィードバック: 試験運用で得たデータを基にシステムの調整や追加機能の検討。
(4) トレーニング
システムを最大限に活用するためには、従業員への教育が欠かせません。
- 操作トレーニング: 現場スタッフがスムーズにシステムを操作できるよう実践的な訓練を実施。
- 役職別の教育プログラム: 管理職と現場スタッフで異なる使用目的に応じたトレーニング内容を提供。
- トレーニングの評価: 習熟度テストや現場でのフォローアップを通じて、実際の運用状況を確認。
(5) 本格導入と運用開始
全社的な導入では、以下のステップで確実な運用を目指します。
- 段階的な展開: いきなり全工程で導入するのではなく、徐々に拡大。
- 専任チームの設置: 導入後の運用支援やトラブル対応を担当する専任チームを設置。
- 効果のモニタリング: 導入後一定期間でKPI(主要業績評価指標)を用いて効果を測定。
(6) 継続的な改善
導入はゴールではなく、スタートです。運用中の改善を続けることで、長期的な効果を最大化します。
- データ分析の活用: 生産データを基に継続的な改善ポイントを特定。
- 定期的なシステムアップデート: 最新の技術や業界トレンドに対応。
- 現場からのフィードバック収集: 実際の使用感や課題をヒアリングし、運用改善に役立てます。
このプロセスを確実に実行することで、生産管理システムの導入効果を最大化し、製造業における競争力の向上を図ることができます。
生産管理システムの導入事例
事例1: 在庫管理の効率化を実現した中小製造業A社
A社は従業員50名規模の金属部品製造会社で、多品種少量生産を行っています。
- 課題: 在庫状況が手作業で管理されており、過剰在庫や欠品が頻発。製造現場が在庫の有無を把握できず、生産効率が低下していました。
- 導入内容: 生産管理システムの在庫管理機能を導入。リアルタイムで在庫状況を把握できるシステムを整備し、在庫データを生産計画と連動させました。
- 導入効果: 在庫回転率が20%向上。欠品による生産停止が大幅に削減。倉庫スペースの最適化により運用コストを10%削減。
- 現場の声: 在庫が見える化され、現場での意思決定がスムーズになりました。
事例2: 生産計画精度の向上を達成した大手製造業B社
B社は従業員500名以上を抱える自動車部品メーカーで、厳しい納期管理が求められる企業です。
- 課題: 生産計画がエクセルで管理されており、需要変動や突発的な変更に対応しきれない状況でした。これにより納期遅延やコスト超過が発生していました。
- 導入内容: 生産計画機能を強化した生産管理システムを導入。需要予測をAIで分析し、生産スケジュールを自動で最適化する仕組みを構築。
- 導入効果: リードタイムが15%短縮。納期遵守率が95%に向上。人為的な計画ミスが削減され、業務効率が20%向上。
- 現場の声: スケジュール調整の手間が激減し、余剰リソースを品質改善に充てられるようになりました。
事例3: 品質向上を実現した食品製造業C社
C社は冷凍食品を生産する中堅企業で、顧客からの品質要求が厳しい業界に属しています。
- 課題: 品質トラブルが頻発し、顧客からのクレームが増加。品質管理が個別部門でバラバラに行われており、トレーサビリティが確保できていませんでした。
- 導入内容: 品質管理機能とトレーサビリティ機能を統合した生産管理システムを導入。製造データを一元化し、製品ごとの履歴を追跡可能にしました。
- 導入効果: クレーム件数が導入1年で30%減少。品質トラブル発生時の対応時間が50%短縮。顧客からの信頼が回復し、新規受注が増加。
- 現場の声: 品質データが一目で分かり、問題解決が迅速に行えるようになりました。
これらの事例から分かるように、生産管理システムはさまざまな課題を解決し、企業の競争力を高める重要な役割を果たしています。
まとめ
生産管理システムは、製造業における効率化と競争力向上の鍵となるツールです。自社の課題を明確にし、適切なシステムを導入することで、業務の可視化やコスト削減、品質向上といった多くのメリットを享受できます。生産管理の効率化を目指す企業にとって、最適なシステム選定は重要なステップです。
CATEGOIRES
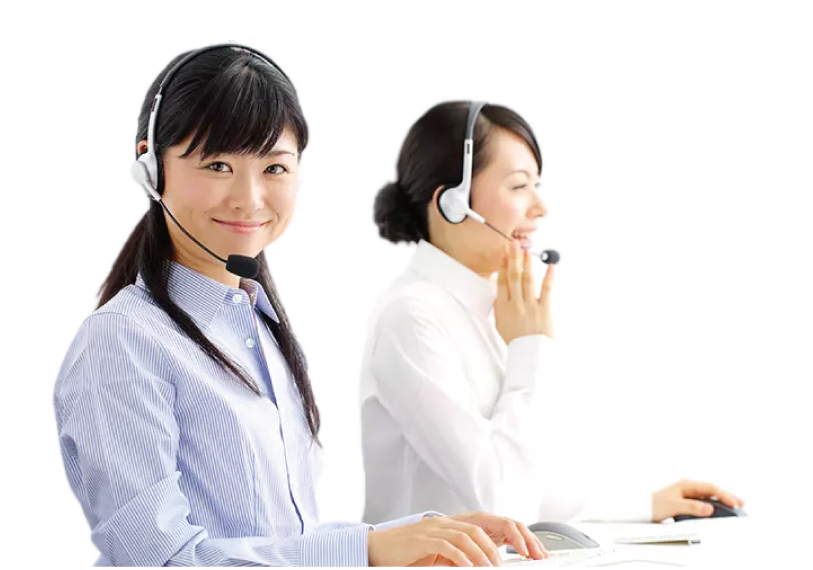
Simpflexに関するお問い合わせはこちら
資料請求と無料デモのお申込みを受け付けています。ご参考までにご覧いただくだけでも構いませんので、是非お気軽にお申し込みください。資料請求では、価格や機能をまとめた詳細資料を最短翌日でお届けいたします。